We Help You Navigate the Unknown. With Informed Perspectives.
Start exploring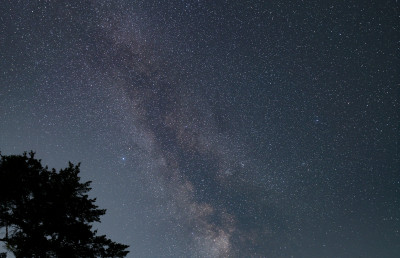
Established in 1995, our firm specializes in advising technology companies on market dynamics, emerging technologies, and forward-looking strategies.
Drawing on decades of experience and a trusted international network, we deliver actionable insights for growth — whether it’s crafting market entry strategies, identifying product requirements and their commercial potential, or supporting strategic purchasing decisions.
In addition to our advisory work, we actively connect our clients with new business partners and have successfully facilitated several joint ventures and M&A transactions.
Our global reach is evidenced by a team with expertise across Europe, North America, Brazil, and India. This international scope is further bolstered by our offices in Germany and China, as well as a partnership in Southeast Asia.
Learn more about what we do and who we are.
The team from Stieler helped us formulate and refine the strategy to grow our robotics business in China. It was clear that Georg and his team knew the markets and customers in China very well and they challenged us to face the reality of rising domestic competition to our products there. They are a top-notch team and deliver valuable insights.
Gregory Smith
President and CEO, Teradyne